Elixir entre o moldeado de silicona e o moldeado por inxección: axustar os procesos ás necesidades do proxecto
No ámbito da fabricación, a selección dos procesos de moldeo é unha decisión crítica, que inflúe no resultado, custo e eficiencia dun proxecto.Dous métodos moi utilizados, o moldeado de silicona e o moldeado por inxección, cada un trae o seu propio conxunto de vantaxes á mesa.Afondemos nos beneficios de cada proceso para comprender mellor cando e por que brillan:
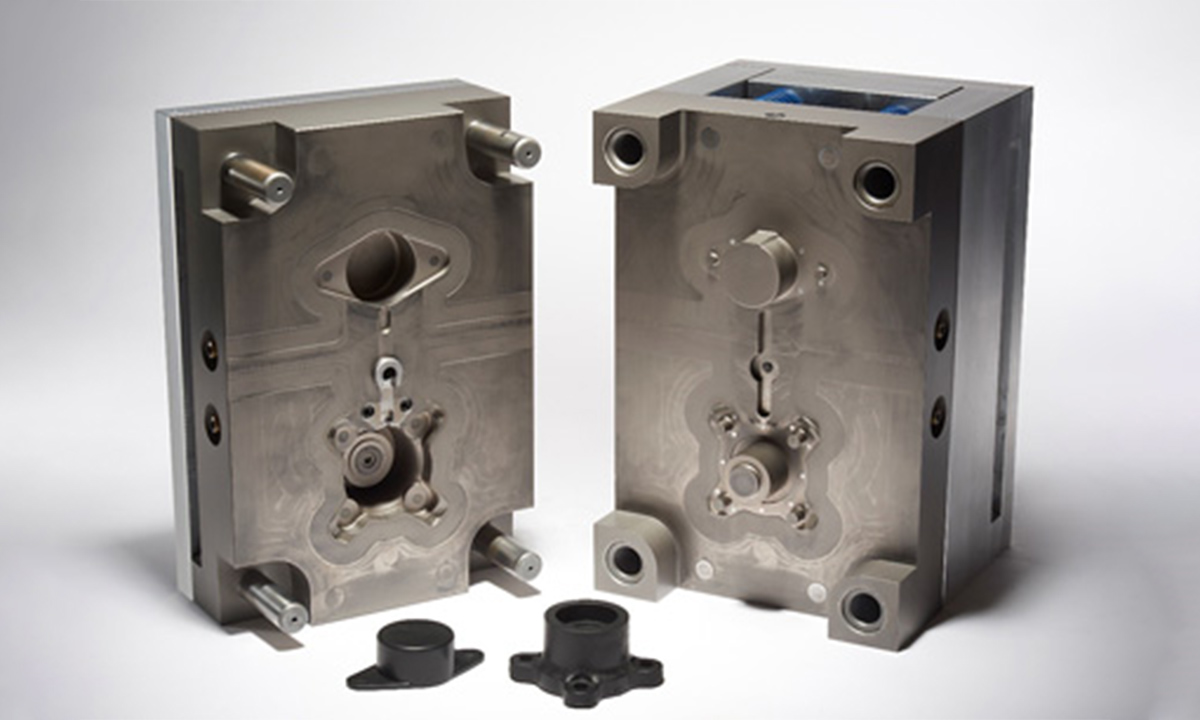
Moldeo por inxección
Moldeo de silicona: elaboración de precisión con flexibilidade
1. Versatilidade: os moldes de silicona teñen flexibilidade, o que lles permite capturar detalles complicados con precisión.Isto fai que sexan ideais para elaborar pezas complexas e delicadas, atendendo a industrias nas que as complexidades do deseño son primordiales.
2. Ferramentas de baixo custo: as ferramentas para moldes de silicona son notablemente menos caras que as ferramentas de moldaxe por inxección.Esta vantaxe de custo sitúa o moldeado de silicona como unha solución rendible, especialmente beneficiosa para pequenas series de produción ou fases de prototipado.
3. Tempos de entrega curtos: os moldes de silicona pódense fabricar rapidamente, ofrecendo unha resposta rápida para proxectos con requisitos sensibles ao tempo.Isto convérteos nunha opción óptima para os esforzos que esixen velocidade sen comprometer a calidade.
4. Compatibilidade de materiais: os moldes de silicona presentan compatibilidade cunha ampla gama de materiais, desde resinas e escumas ata metais de baixa temperatura.Esta flexibilidade nas opcións de materiais mellora a súa idoneidade para diversas necesidades de fabricación.
5. Baixa presión: o proceso de moldeo da silicona implica unha presión máis baixa, polo que é especialmente adecuado para materiais sensibles a altas presións e temperaturas.Este enfoque suave garante a integridade dos materiais delicados.
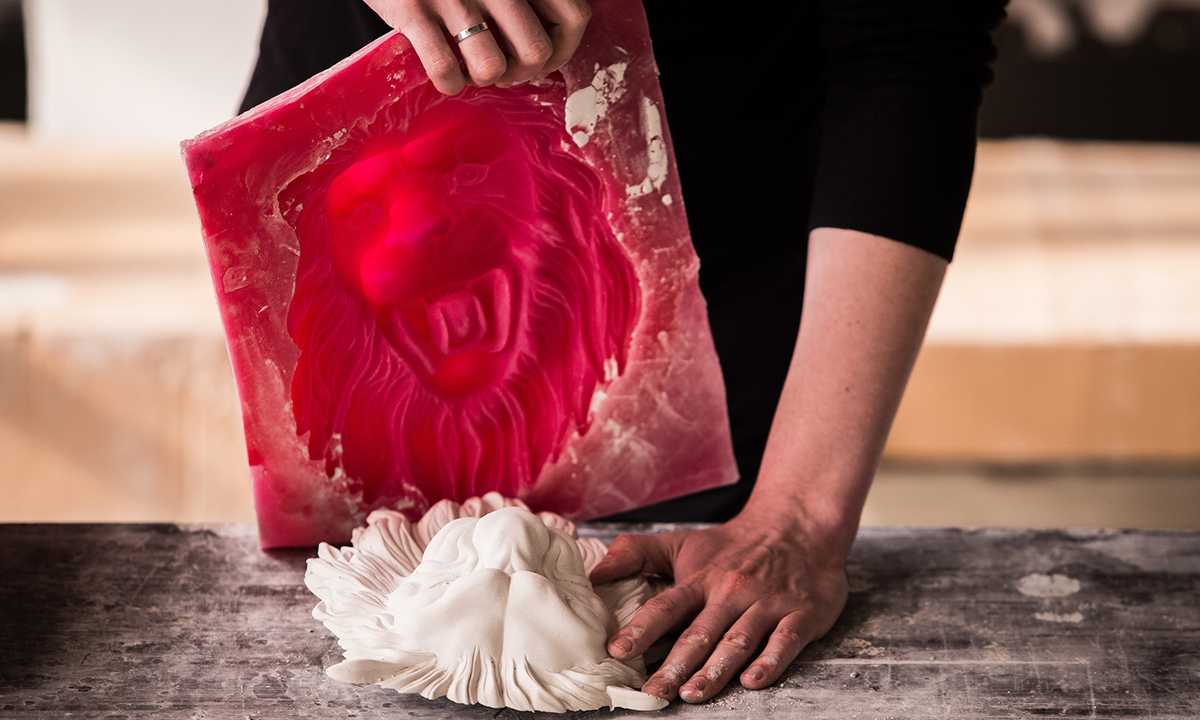
Moldeo de silicona
Moldeo por inxección: a eficiencia da precisión de alto volume
1. Produción de alto volume: a moldaxe por inxección toma o liderado cando se trata de produción de gran volume.A súa eficiencia e rapidez, unha vez que a ferramenta inicial está no seu lugar, permite a produción automatizada de grandes cantidades de pezas, o que o converte nunha opción preferida para a fabricación en masa.
2. Consistencia e precisión: o proceso de moldaxe por inxección garante unha alta repetibilidade e precisión, factores cruciais para industrias onde a calidade consistente en todas as pezas producidas non é negociable.Esta fiabilidade é especialmente valorada en sectores como a automoción e a electrónica.
3. Ampla gama de materiais: o moldeado por inxección admite unha ampla gama de materiais, que abarca plásticos de enxeñería, elastómeros e metais.Esta versatilidade faino aplicable a un amplo espectro de industrias e aplicacións.
4. Formas complexas e tolerancias estreitas: a precisión alcanzable co moldeado por inxección permite a creación de xeometrías complexas e tolerancias estreitas.Isto fai que sexa o método de elección para pezas que requiren un alto nivel de detalle e precisión.
5. Eficiencia de custos (para tiradas grandes): aínda que o custo inicial de ferramentas pode ser maior, o custo por peza diminúe significativamente con cantidades de produción máis grandes.Esta eficiencia de custos nas operacións a gran escala sitúa o moldeado por inxección como a opción preferida para aqueles que buscan economías de escala.
Elixir con sabedoría: relacionar o proceso co proxecto
En conclusión, a decisión entre o moldeado de silicona e o moldeado por inxección depende de varios factores, incluíndo a cantidade desexada de pezas, a complexidade do deseño, os requisitos de materiais, as especificacións de precisión e as limitacións orzamentarias.Para tiradas máis pequenas, prototipos ou pezas complicadas, pode prevalecer a flexibilidade e a rendibilidade do moldeado de silicona.Non obstante, cando se busca unha produción de gran volume, calidade consistente e rendibilidade, o moldeado por inxección adoita aparecer como a solución óptima.A clave reside en comprender os puntos fortes únicos de cada proceso e aliñalos coas necesidades específicas do proxecto en cuestión.
Hora de publicación: 19-xan-2024